Existen muchos tipos de láminas de plástico con una amplia gama de usos. Actualmente, los principales tipos son el cloruro de polivinilo, el poliestireno y el poliéster (PET). La lámina de PET tiene un buen rendimiento y cumple con los requisitos del índice nacional de higiene para productos moldeados y los requisitos internacionales de protección ambiental. Pertenecen a la tabla de protección del medio ambiente. Actualmente, los envases deben cumplir con los requisitos de reciclaje y protección ambiental, por lo que la demanda de láminas de PET es cada vez mayor. Este artículo analiza principalmente el proceso de producción y los problemas comunes de las láminas de PET.
Tecnología de producción de láminas de PET:
(1) lámina de PET
Al igual que otros plásticos, las propiedades de las láminas de PET están estrechamente relacionadas con el peso molecular. El peso molecular está determinado por la viscosidad intrínseca. Cuanto mayor sea la viscosidad intrínseca, mejores serán las propiedades físicas y químicas, pero habrá poca fluidez y dificultad de formación. Cuanto menor sea la viscosidad intrínseca, peores serán las propiedades físicas y químicas y la resistencia al impacto. Por lo tanto, la viscosidad intrínseca de la lámina de PET debe ser de 0,8 dl/g-0,9 dl/g.
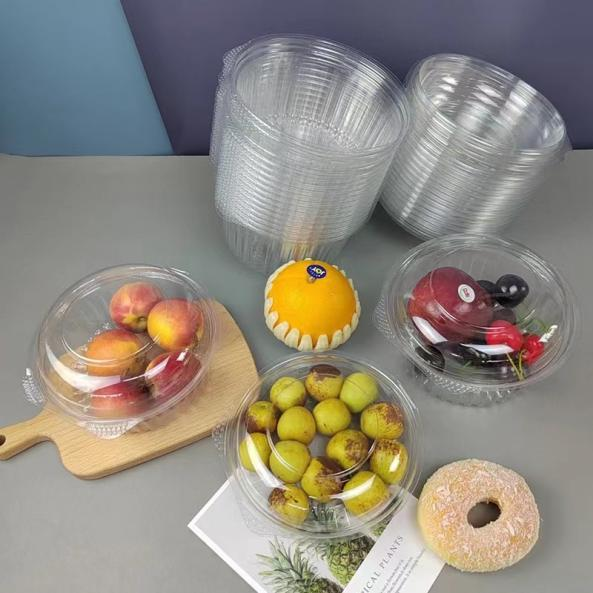
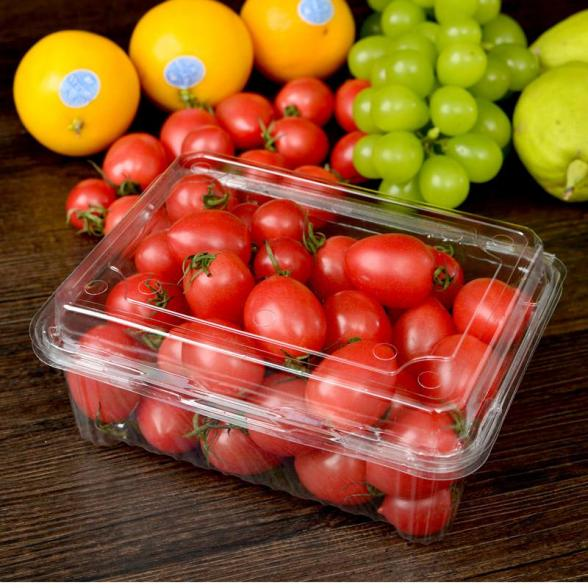
(2) Flujo del proceso de producción
el principalequipos de producción de láminas de PETincluye torres de cristalización, torres de secado, extrusoras, cabezales de troquelado, calandrias de tres rodillos y bobinadoras. El proceso de producción es: cristalización de materia prima-secado-extrusión plastificación-extrusión moldeo-calandrado y conformación-bobinado de productos.
1. Cristalización. Las rodajas de PET se calientan y cristalizan en la torre de cristalización para alinear las moléculas y luego aumentan la temperatura de transición vítrea de las rodajas para evitar la adhesión y la obstrucción de la tolva durante el proceso de secado. La cristalización es a menudo un paso esencial. La cristalización tarda entre 30 y 90 minutos y la temperatura es inferior a 149°C.
2.Secar. A altas temperaturas, el agua hidrolizará y degradará el PET, lo que dará como resultado una reducción de su adhesión característica, y sus propiedades físicas, especialmente la resistencia al impacto, disminuirán a medida que disminuye el peso molecular. Por lo tanto, antes de fundir y extruir, el PET debe secarse para reducir el contenido de humedad, que debe ser inferior al 0,005%. Para el secado se utiliza un secador deshumidificador. Debido a la higroscopicidad del material PET, cuando el agua penetra profundamente en la superficie de la rebanada, se formarán enlaces moleculares y otra parte del agua penetrará profundamente en la rebanada, dificultando el secado. Por lo tanto, no se puede utilizar aire caliente normal. Se requiere que el punto de rocío del aire caliente sea inferior a -40 °C y el aire caliente ingresa a la tolva de secado a través de un circuito cerrado para un secado continuo.
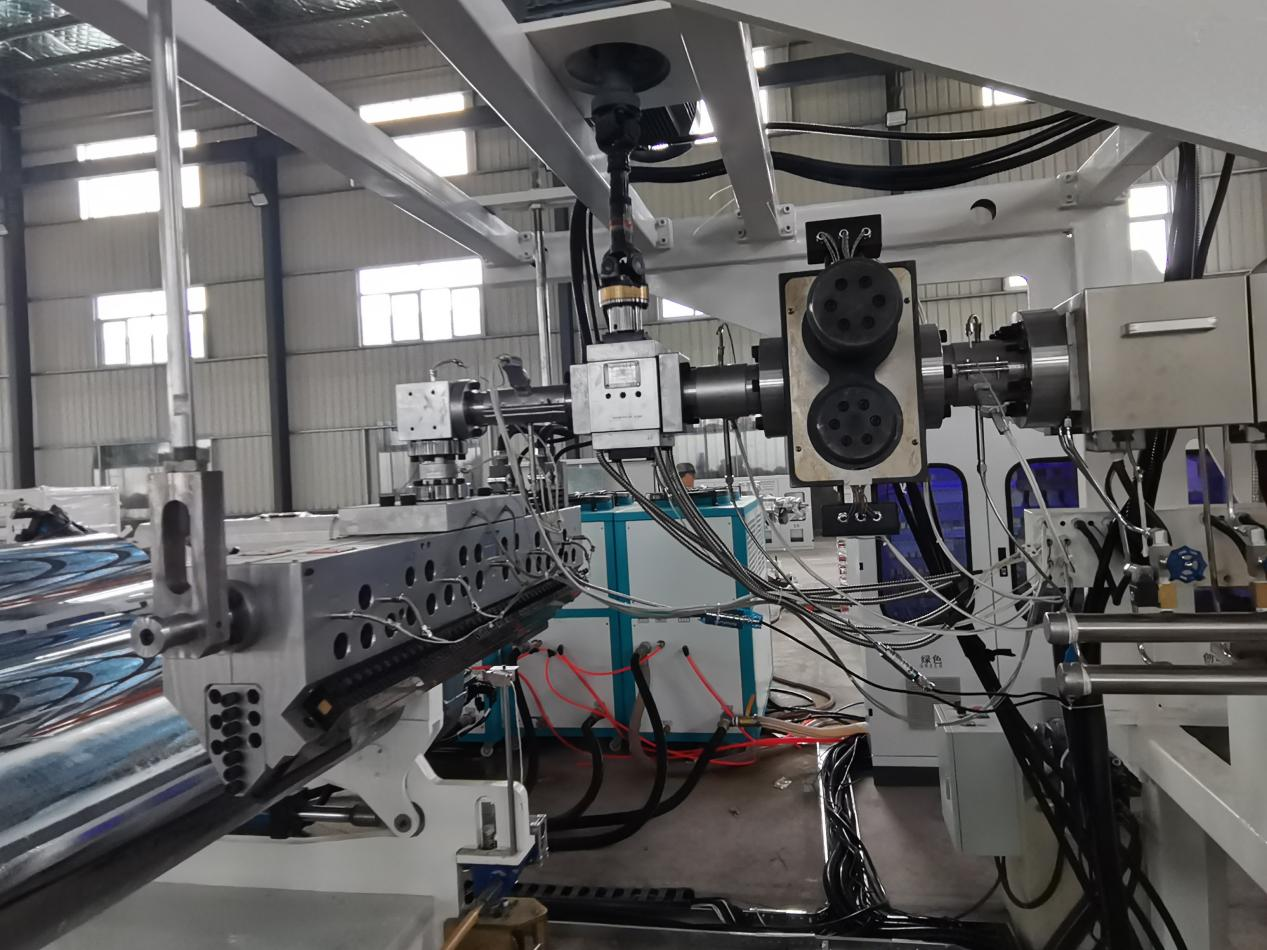
3. Apretar. Después de la cristalización y el secado, el PET se transforma en un polímero con un punto de fusión evidente. La temperatura de moldeo del polímero es alta y el rango de control de temperatura es estrecho. Se utiliza un tornillo de barrera específico de poliéster para separar las partículas no fundidas de la masa fundida, lo que ayuda a mantener un proceso de cizallamiento más prolongado y aumenta el rendimiento de la extrusora. Adopta un troquel de labio flexible con varilla de acelerador aerodinámica. La cabeza del molde es cónica. Los canales aerodinámicos y los labios del troquel sin rayones indican que el acabado debe ser bueno. El calentador de molde tiene funciones de drenaje y limpieza.
4.Enfriamiento y conformación. Después de que la masa fundida sale del cabezal, ingresa directamente a la calandria de tres rodillos para su calandrado y enfriamiento. La distancia entre la calandria de tres rodillos y el cabezal de la máquina generalmente se mantiene en aproximadamente 8 cm, porque si la distancia es demasiado grande, el tablero se combará y arrugará fácilmente, lo que resultará en un acabado deficiente. Además, debido a la larga distancia, la disipación de calor y el enfriamiento son lentos y el cristal se vuelve blanco, lo que no favorece la rodadura. La unidad de calandrado de tres rodillos consta de rodillos superior, medio e inferior. El eje del rodillo central está fijo. Durante el proceso de enfriamiento y calandrado, la temperatura de la superficie del rodillo es de 40°c-50°c. El eje de los rodillos superior e inferior puede moverse hacia arriba y hacia abajo.
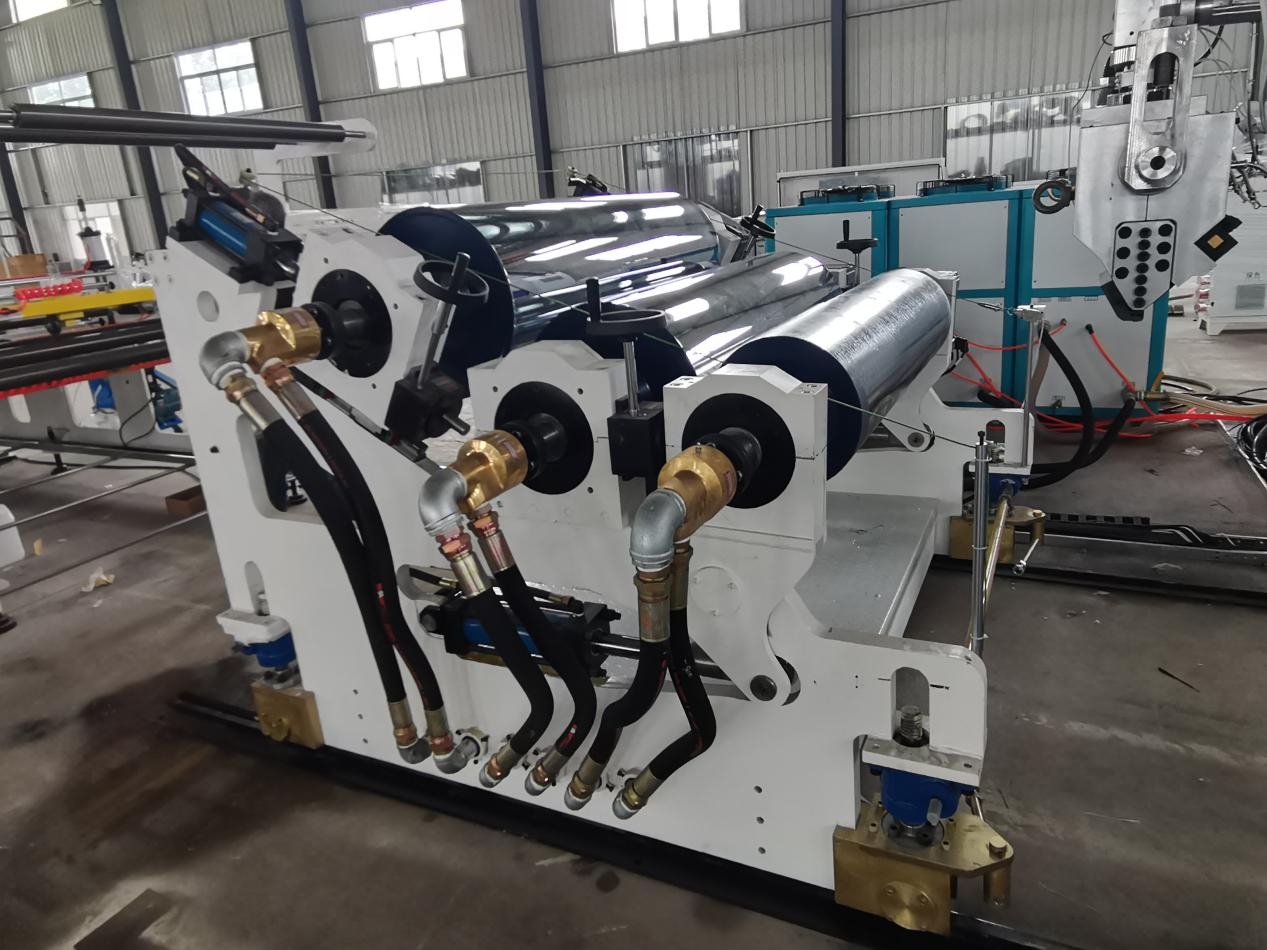
Hora de publicación: 28 de septiembre de 2023